Rotary PTFE and Spring Energised Seals
Standard Profiles
Moontown solid PTFE Lip seals provide the designer with a significant improvement in performance over elastomer lip seals at a much lower cost than a mechanical face seal.
- Temperature range: 20°C to 250°C
- Pressure up to 30 bar
- High chemical resistance
- Metal support ring for high temperatures
- Low friction
- Surface speeds up to 25 m/s
- Dry running or abrasive media
- Easy to install and replace
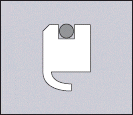
TYPE M50
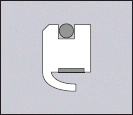
TYPE M51
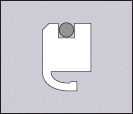
TYPE M52
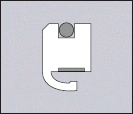
TYPE M53
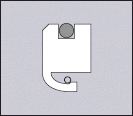
TYPE M54
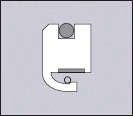
TYPE M55
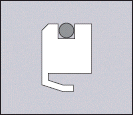
TYPE M56
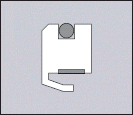
TYPE M57
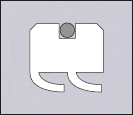
TYPE M58
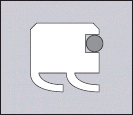
TYPE M59
Rotary Seals Hardware Design
Rotary Seal Selection Chart
Shaft Material and Hardness | Finish |
---|---|
Cast Iron or Hardenable Steel -40 to 65 HRc with hydraulic oil up to 15 bar |
Shaft Ra 0.3 - 0.5 µm for lubricated applications Bore or O-Ring Side Ra = 0.8 - 1.6 µm |
Hardware Dimensions
NOM |
NOM BORE B DIM |
SEAL WIDTH W DIM |
---|---|---|
8 | 22 | 7 |
24 | ||
26 | ||
9 | 22 | 7 |
24 | ||
26 | ||
10 | 22 | 7 |
24 | ||
26 | ||
11 | 22 | 7 |
26 | ||
12 | 22 | 7 |
24 | ||
28 | ||
30 | ||
14 | 24 | 7 |
28 | ||
30 | ||
35 | ||
15 | 26 | 7 |
30 | ||
32 | ||
35 | ||
16 | 28 | 7 |
30 | ||
32 | ||
35 | ||
17 | 28 | 7 |
30 | ||
32 | ||
35 | ||
40 | ||
18 | 30 | 7 |
32 | ||
35 | ||
40 | ||
20 | 30 | 7 |
32 | ||
35 | ||
40 | ||
47 | ||
22 | 32 | 7 |
35 | ||
40 | ||
47 | ||
24 | 35 | 7 |
37 | ||
40 | ||
47 | ||
25 | 35 | 7 |
40 | ||
42 | ||
47 | ||
52 | ||
26 | 37 | 7 |
42 | ||
47 |
NOM SHAFT S DIM |
NOM BORE B DIM |
SEAL WIDTH W DIM |
---|---|---|
28 | 40 | 7 |
47 | ||
52 | ||
30 | 40 | 7 |
42 | ||
47 | ||
52 | ||
62 | 8 | |
32 | 45 | 7 |
47 | ||
52 | ||
35 | 47 | 7 |
50 | ||
52 | ||
62 | 8 | |
36 | 47 | 7 |
50 | ||
52 | ||
62 | 8 | |
38 | 52 | 7 |
55 | 8 | |
62 | ||
40 | 52 | 7 |
55 | 8 | |
60 | ||
62 | ||
72 | ||
42 | 55 | 8 |
60 | ||
62 | ||
72 | ||
45 | 60 | 8 |
62 | ||
65 | ||
72 | ||
48 | 62 | 8 |
65 | ||
72 | ||
50 | 65 | 8 |
68 | ||
72 | ||
80 | ||
52 | 68 | 8 |
72 | ||
55 | 70 | 8 |
72 | ||
80 | ||
85 | 10 | |
56 | 70 | 8 |
72 | ||
80 | ||
85 | 10 | |
58 | 72 | 8 |
80 | ||
60 | 75 | 8 |
80 | ||
85 | 10 | |
90 |
NOM SHAFT S DIM |
NOM BORE B DIM |
SEAL WIDTH W DIM |
---|---|---|
62 | 80 | 8 |
85 | 10 | |
90 | ||
63 | 85 | 10 |
90 | ||
65 | 85 | 10 |
90 | ||
100 | ||
68 | 90 | 10 |
100 | ||
70 | 90 | 10 |
100 | ||
72 | 95 | 10 |
100 | ||
75 | 95 | 10 |
100 | ||
78 | 100 | 10 |
80 | 100 | 10 |
110 | 12 | |
85 | 110 | 12 |
120 | ||
90 | 110 | 12 |
120 | ||
95 | 120 | 12 |
125 | ||
100 | 120 | 12 |
125 | ||
130 | ||
105 | 130 | 12 |
140 | ||
110 | 130 | 12 |
140 | ||
115 | 140 | 12 |
150 | ||
120 | 150 | 12 |
160 | ||
125 | 150 | 12 |
160 | ||
130 | 160 | 12 |
170 | 15 | |
135 | 170 | 15 |
140 | 170 | 15 |
145 | 175 | 15 |
150 | 180 | 15 |
160 | 190 | 15 |
170 | 200 | 15 |
180 | 210 | 15 |
190 | 220 | 15 |
200 | 230 | 15 |
- Bore and shaft dimensions are based on DIN Standards 3760.
- Moontown can manufacture non-standard sizes to fit your existing hardware.
- Please consult Moontown for further details.
- This table also applies to our metal cased lip seals.
- Please see seperate sheet for metal cased PTFE Lip Seal.